タイトルと離れているのは承知の上だが、作った基板の部品実装強度に問題が出てきたようだ。課題はテンションのかかるDCJACKとUSBコネクターでどちらも給電用に用いたものなのだがスルーホールでなくて、フィットした角穴でもない大きな径を合わせただけのランドへのはんだ付けがピンポイントになるのは自明の理でさすがに強度不足だわ。
対応策として現在のツールチェーンでの折り合いを図ることにした。
CAD自体は、試作目的ではPCBEを用いているのだが外形に限っては角穴が出来そうなので、大きな角ランドに角穴をあけるという方向性でパラメータを振ってみてツールとして穴加工に合意する点を探した。
この基板では、切り欠きやインシュロックを通すための角穴は付けていた。そこで分かったことは、Oriminでは外形線として角穴は許容するものの斜め線や多角形は許容しないらしい。縁に出来るだけ近くに寄せた角穴を最後に切り落とすという作戦にした。
角穴ということの定義は描画時点で穴になっていないといけないらしく少なくも0.2mm以上の間隙が出来るようにしないと切削線が重なっている状況では許してくれない。また、そうした際に外形加工の刃物径とも関連してきていて今回の調査では刃物として外形0.5mmのオリジナルマインド社謹製の土佐昌典FTを利用して所謂一本使いで粗く仕上げる作戦なのだが、加工パラメータにはあえて嘘を入れて0.1mmの刃物ということにした。こうすることでこのツールパスを許容してくれたのだ。Oriminでは加工判定後ツールパスを描画してくれるので、こうした設定がうまく使えるのかどうか予め確認できる。
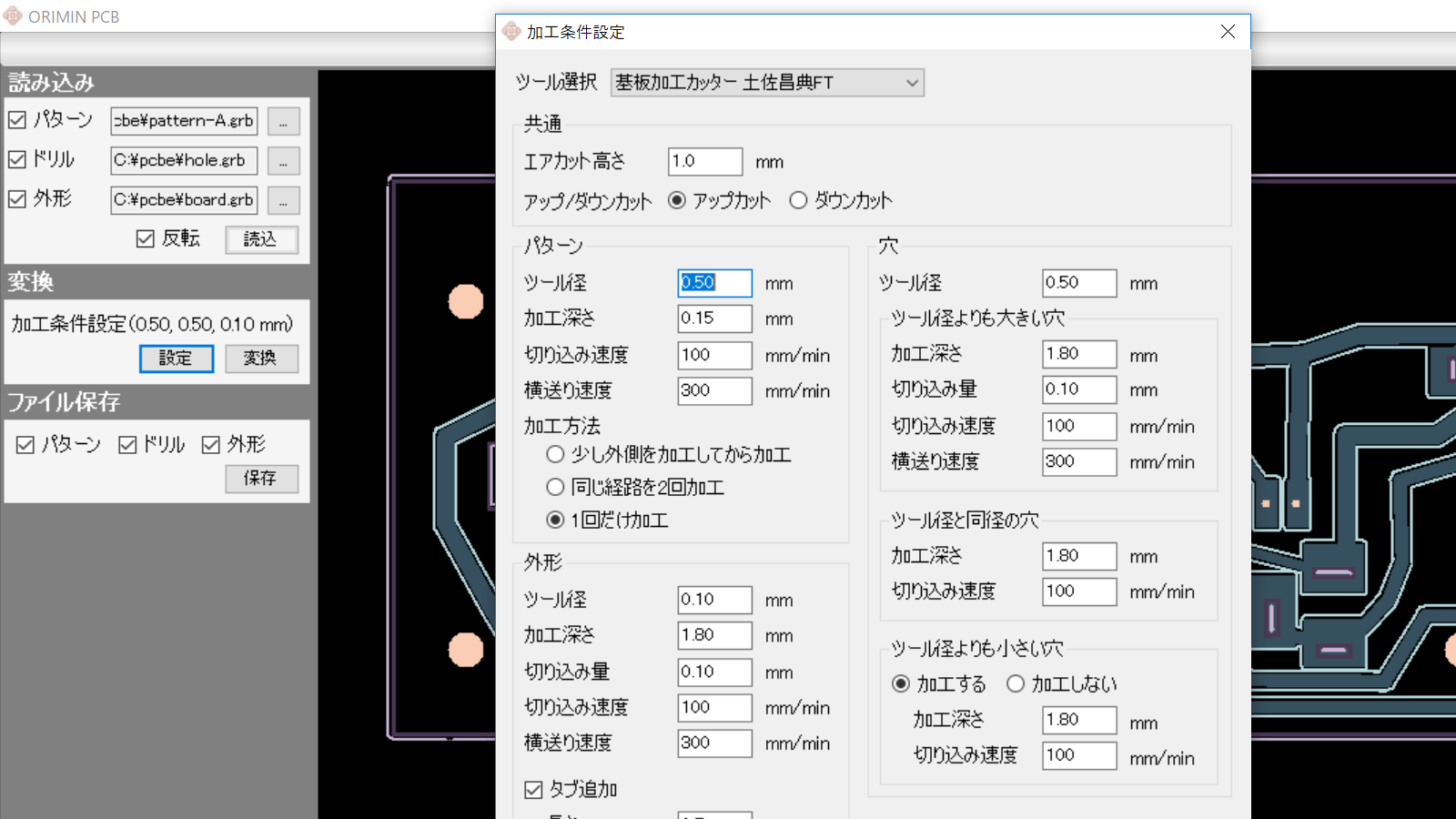
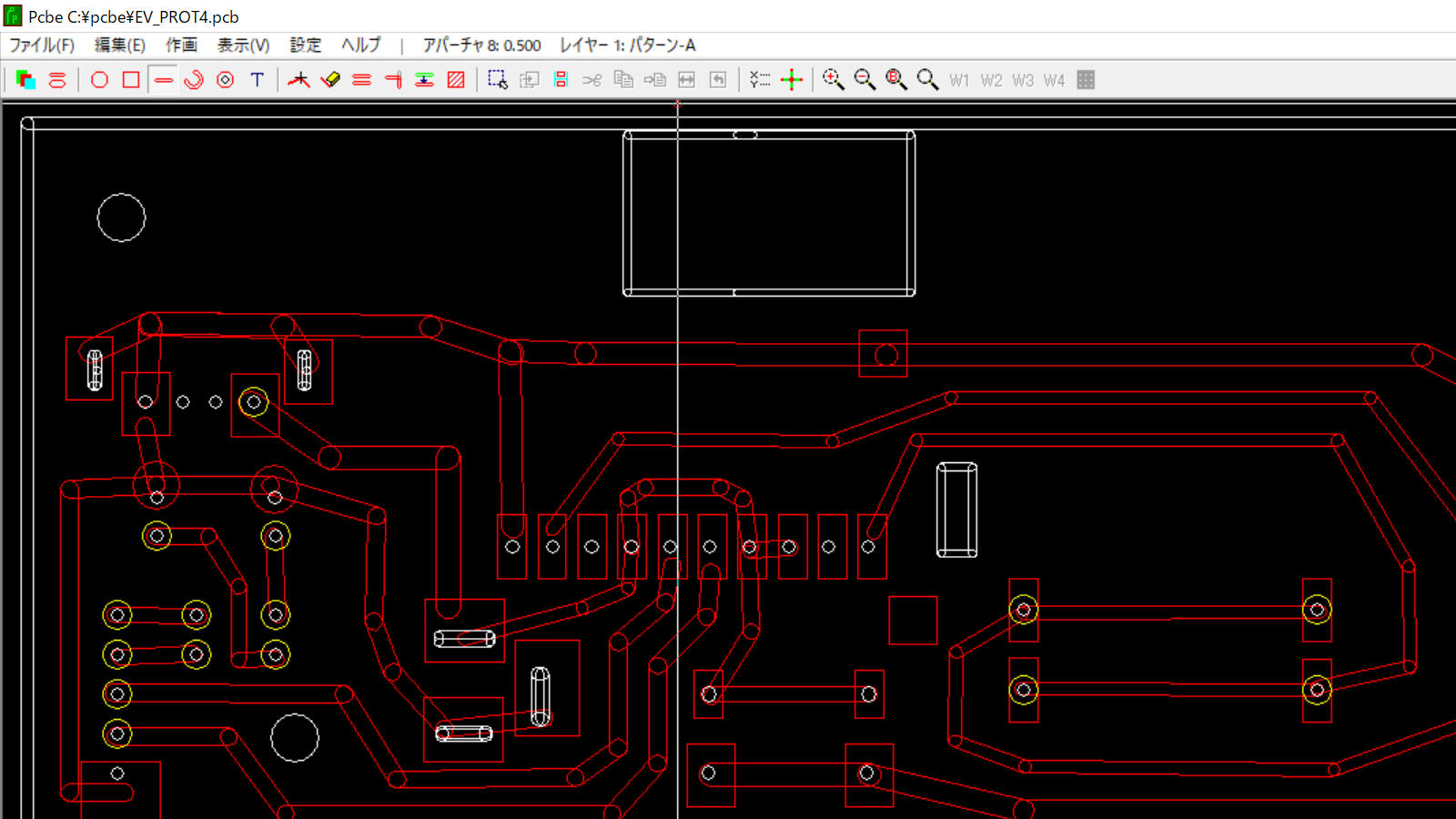
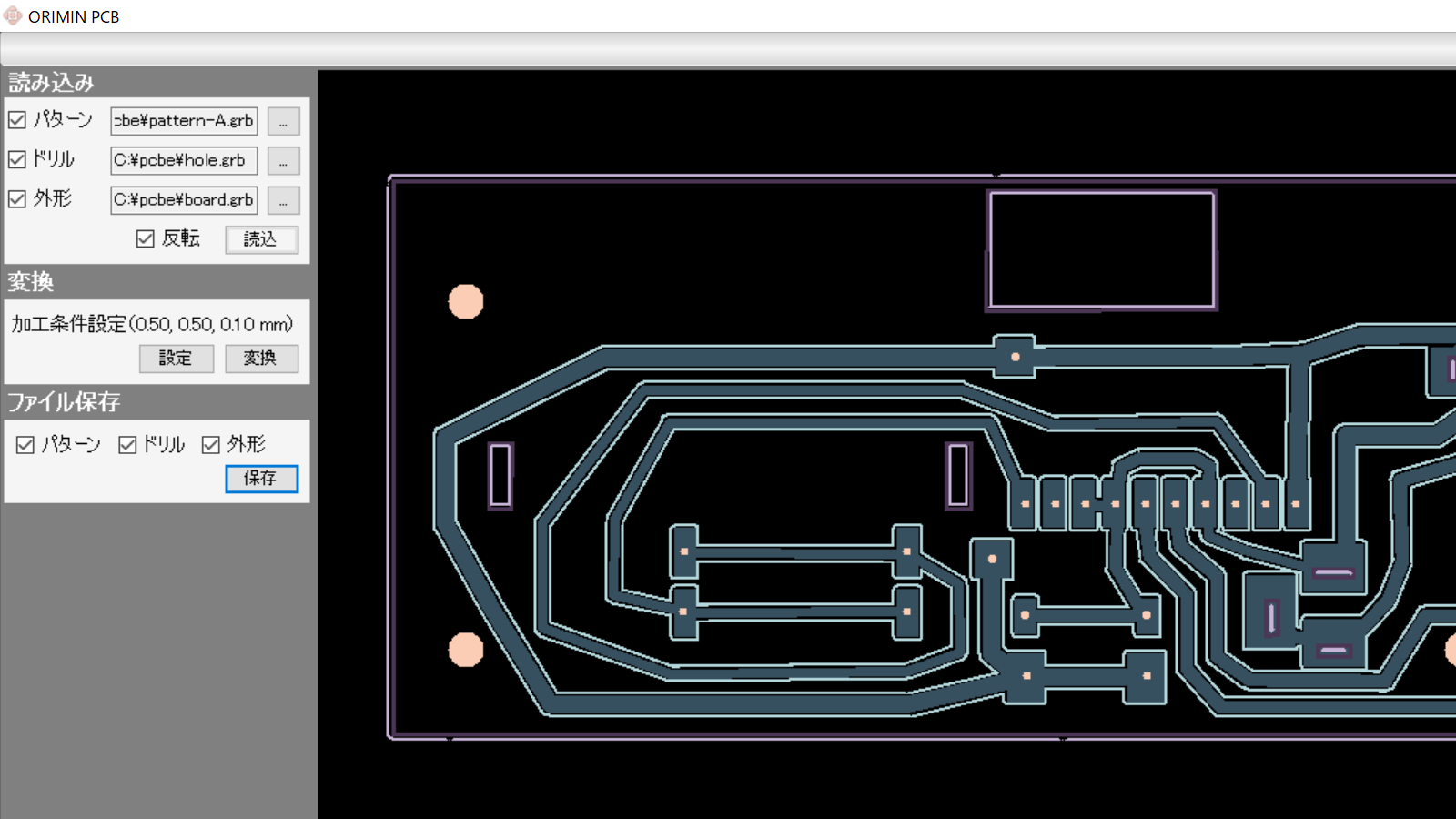