今回のお題は、市販の防水樹脂筐体に収めるある程度数を作ることを想定したモノづくりのお手伝いだ。里の加工で出来ることはしれているのだが、そこはベンチャー会社の人たちにしてみたら他に頼むことよりも出来るだけ作れるものなら最初にどこまで作れるのかは知りたいということらしい。
基板手配は、当初の課題だったが、サイズの問題などからEAGLEからKiCADに移行して新しい機能などを覚えて試作品としてOriminを用いたUSBCNCで削り出して試作評価というフェーズが簡単に崩れてしまった。良くも悪くも今までの使い方がCADというよりもアートワークを手で引いているようなPCBEだったりしていたことから制限を外して挑戦しようということでもあったのだが、試作用もう少し融通の利く環境構築も必要のようだ。
基板がとりあえず、KiCADのアートワーク状況を手コピーしてPCBEのスクリーンにプロットしていくのだがPCBEの柔軟な運用としてプロットポイントを自在に原点調整やピッチ変更が出来るのが幸いしてほどなく出来るのだが、あいにくと強度が必要なUSBコネクタやDCジャックの類の角穴などは折角モデルを使ったのが仇となっていたので丸で近似するしかなかった、作図は簡単だがはんだ付けの苦労はありそうだ。
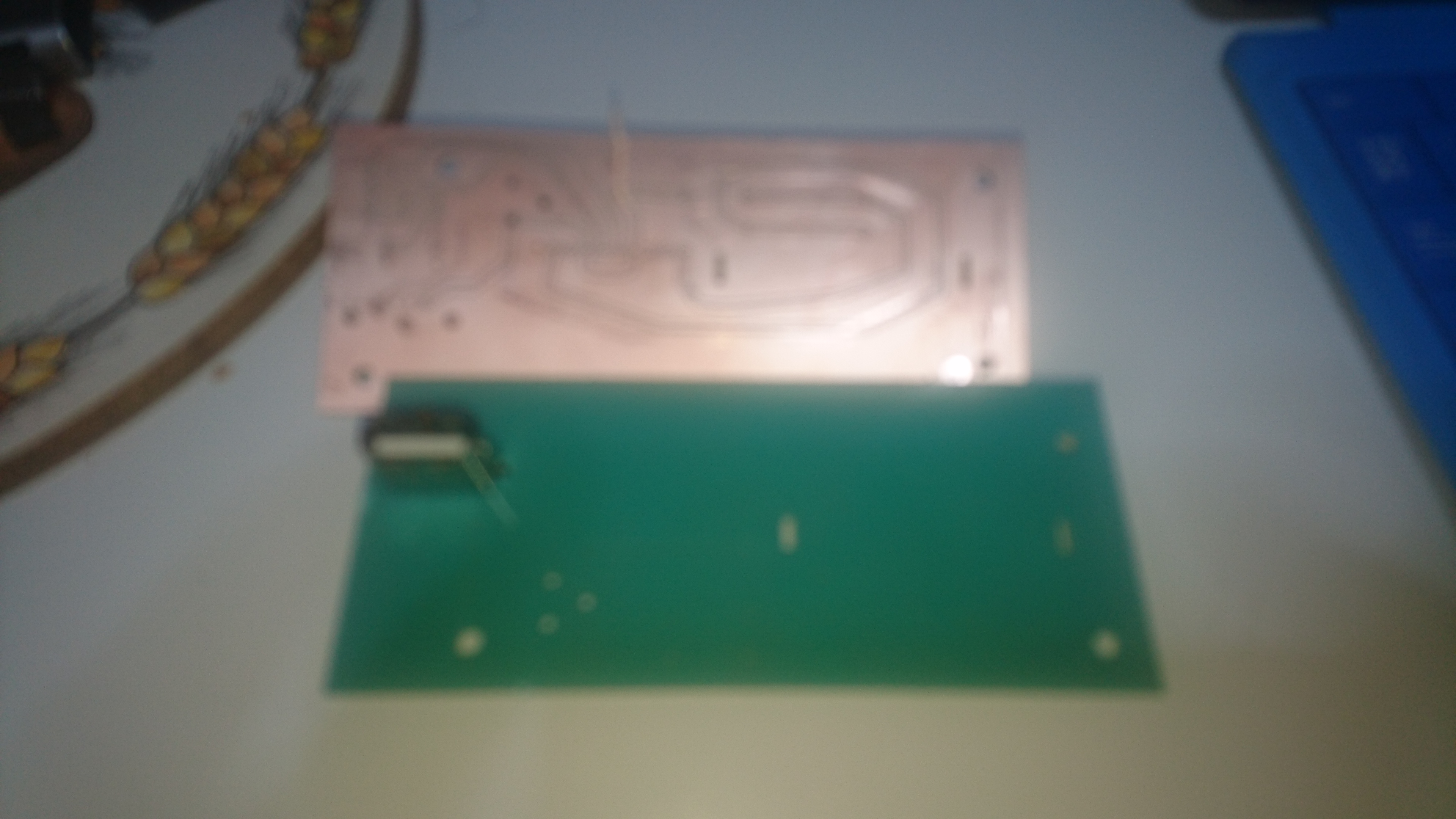
これやArduinoの基板をスペーサーで保持するのだが、その設置用の穴開けが課題になりそうだということは先週のトライアルで分かった。穴あけ位置を指示する樹脂製のテンプレートを作成してそれ越しに穴あけをすることにした。これを作るのは今回は3Dプリンターで少し垂直のガイド性もつくようにした。
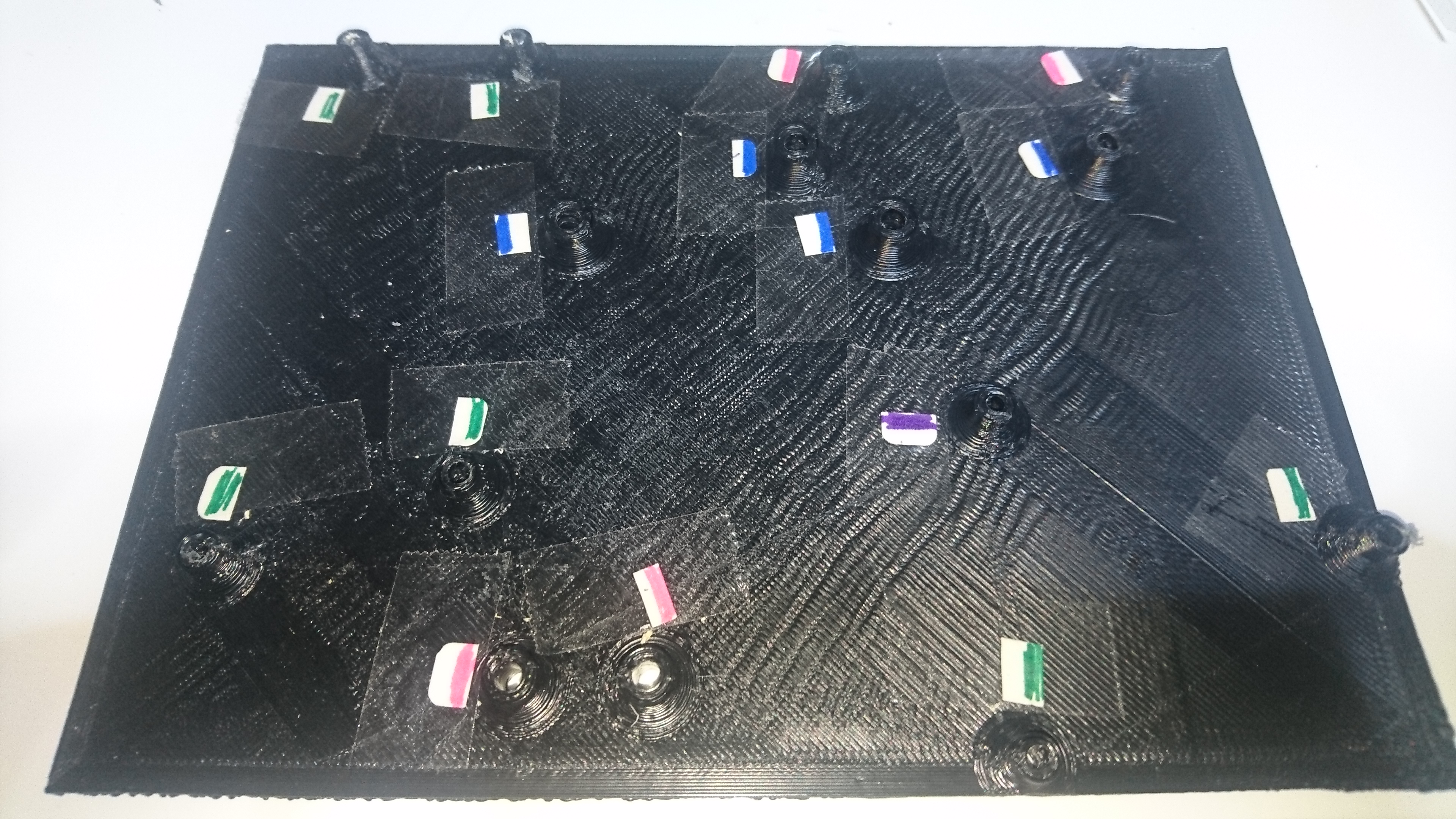
結局Arduino以外も含めて全体のテンプレートが丁度3Dプリンターで作れそうなので穴のサイズごとに色指示のシールを貼って効率が上がるようにしてみた。
Arduino UNOには使えないコーナーピンが一か所あり、設計上は3mmのビスを使うことになっているのだが実際にあたってしまいネジ締めが出来なかったりもしているので、ここは2.6mmのネジを一か所だけ使うようにした。そんなこともあったれして実はバタバタとしたNCデータの流用だった。転写する段階で読み間違えたりしてサイズ位置が合わなかったこともあったので、もう少しレビューを落ち着いてしたほうが良さそうだった。問題のUNOのマウントには樹脂製のスペーサーを使わないと背面のパターンも当たってショートしそうな感じもしたので手持ちのジュラコンのパーツを見つけ出してくみ上げてみた。
明日、全体試験をしてもらって来週はいよいよ顧客先で稼働評価試験となるらしい。